If you’ve spent more than a few days on any car audio-related social media platform, you’ve likely seen someone inquire about a melted wire connection. It’s a common issue that many enthusiasts face, and it’s understandable that not everyone might be well-versed in Ohm’s law from their grade 9 science class. Despite this, the questions and photos keep coming. Let’s explore some reasons behind these melted connections.
Why Do Some Car Audio Wire Connections Melt?
Every type of electrical connection, whether it’s plugging in a toaster to a household socket, plugging a USB cable into your smartphone, or connecting a large-gauge power cable to your car audio amplifier, involves some amount of resistance. In some instances, such as the case of fuses, we can use this resistance to our benefit. In most cases, resistance causes a voltage drop that reduces the power delivered from the source to the load.
Let’s look at a little example. Say we have a large subwoofer amplifier with four AWG power and ground wires connected to the terminal block. Suppose the person who did the installation didn’t tighten the terminal block well. When the amp draws 100 amps of current, we measure 0.5 volts between the wire and the power terminal. A little math tells us that that connection has 0.005 ohms of resistance. Five milliohms of resistance doesn’t sound like much, does it? You definitely couldn’t measure that resistance with an ohmmeter.
If we calculate the power dissipated in that connection, we get 50 watts. While it doesn’t seem like a significant amount of power, 50 watts is a lot of heat. Even more so when it’s confined to a very small location. When spread out across 20 feet of wire or when connected to a heatsink, it’s not a problem. When confined to a little piece of wire and a pot-metal terminal block soldered to a circuit board, it’s a recipe for damage.
If you want to better understand the math we used in the above two paragraphs, check out our Car Audio Masterclass series. Lesson 101.2 deals specifically with basic Ohm’s Law calculations.
In almost every case where a wire heats up, the issue is that there is too much resistance.
What Causes Resistance in Car Audio Connections?
You might think, “OK, I know there was resistance. What caused it? I was sure that connection was tight!” And if you think that, then good for you. There are a few reasons why car audio electrical connections might increase resistance over time.
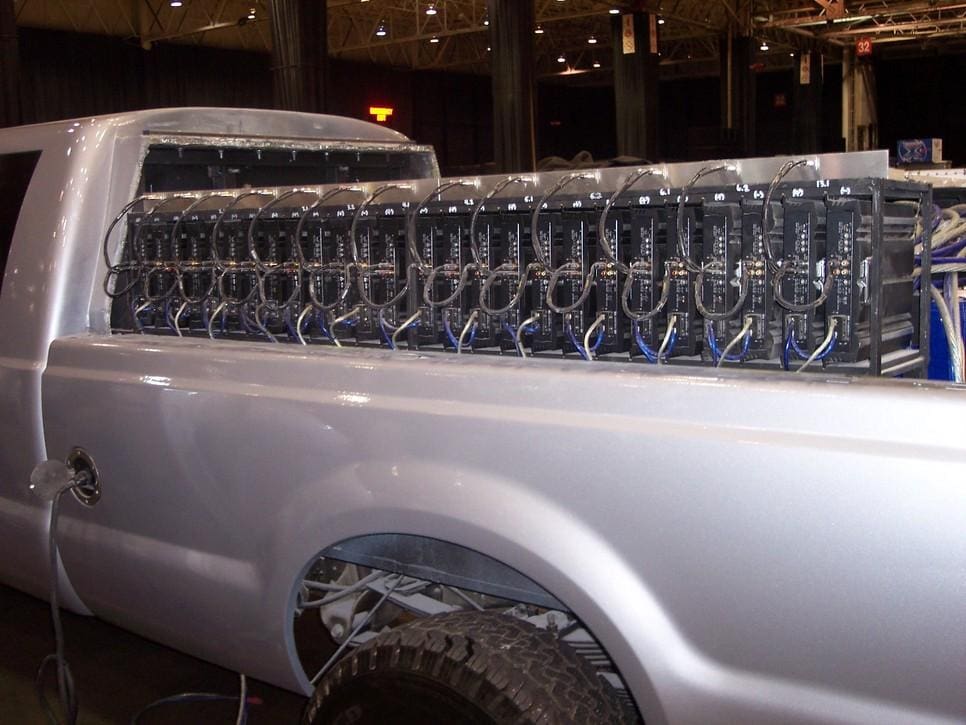
Vibration and Wire Movement
First, we have the issue of vibration. Unlike wiring in your home audio system, a vehicle is always subjected to loads and vibration during regular operation. Accelerating, braking, and going around a corner pull on every electrical connection. Going over bumps, potholes, expansion joints, and manhole covers can often cause impacts that register well into the three G range. A wire pulling on a connection with a force of a few ounces might exert nearly a pound of force.
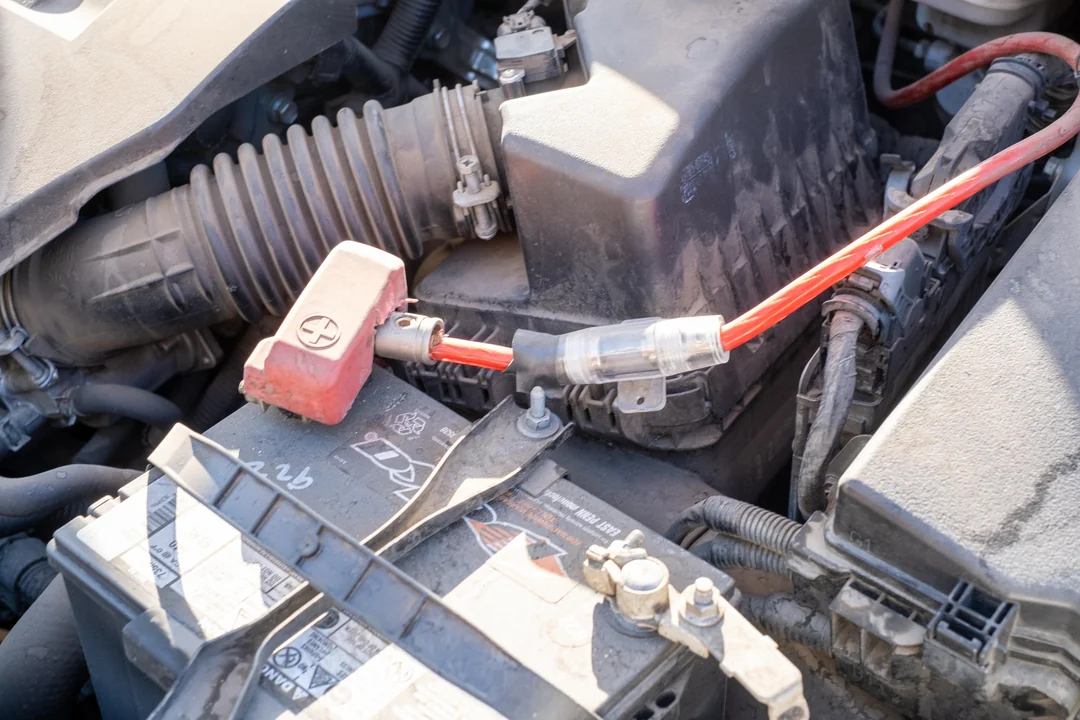
The solution is to ensure the person installing your audio system has supported the wiring so that there is no pressure or load on the connection. How this is accomplished depends on the installation. The wire might need to be secured to an amp rack or to the vehicle.
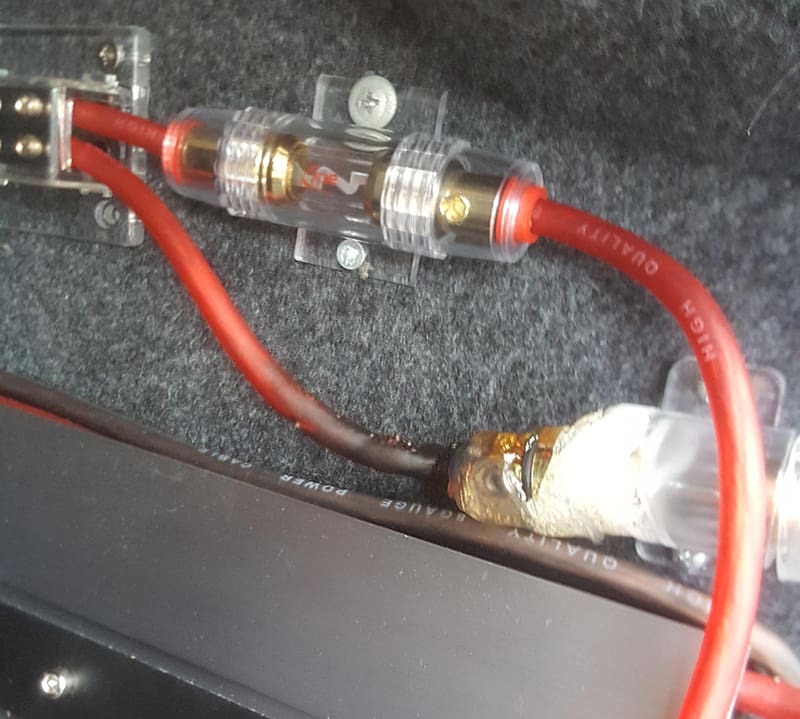
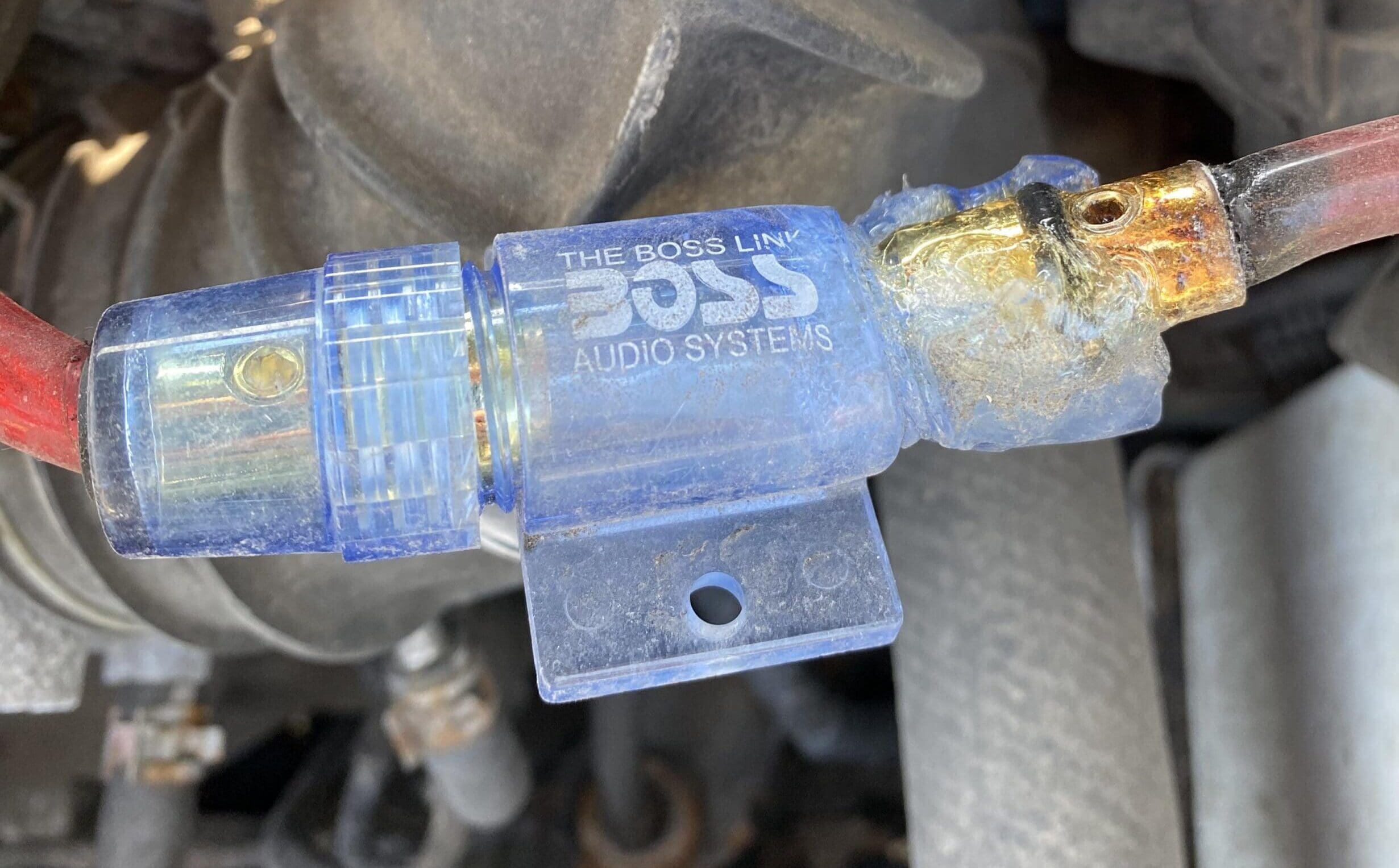
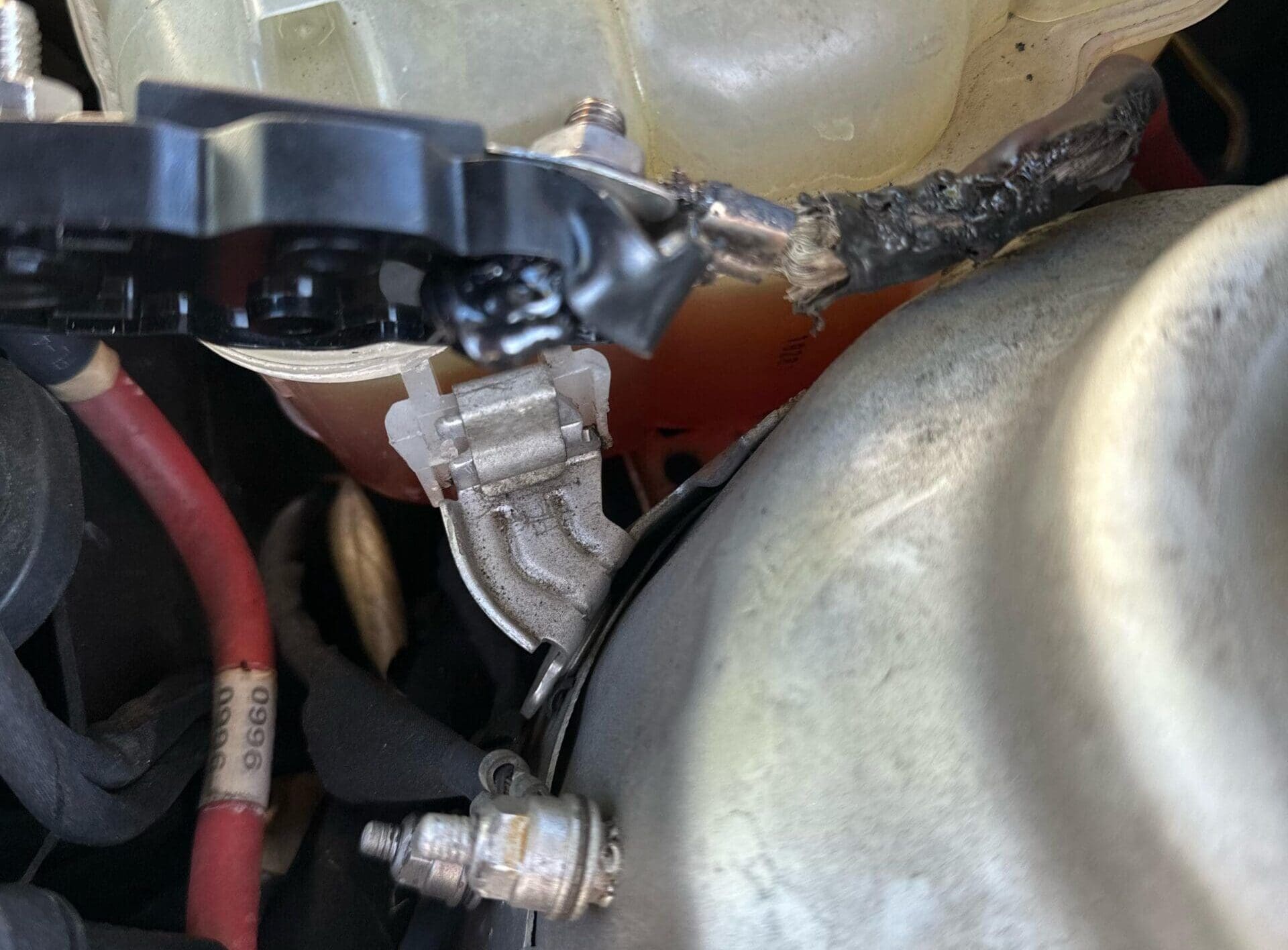
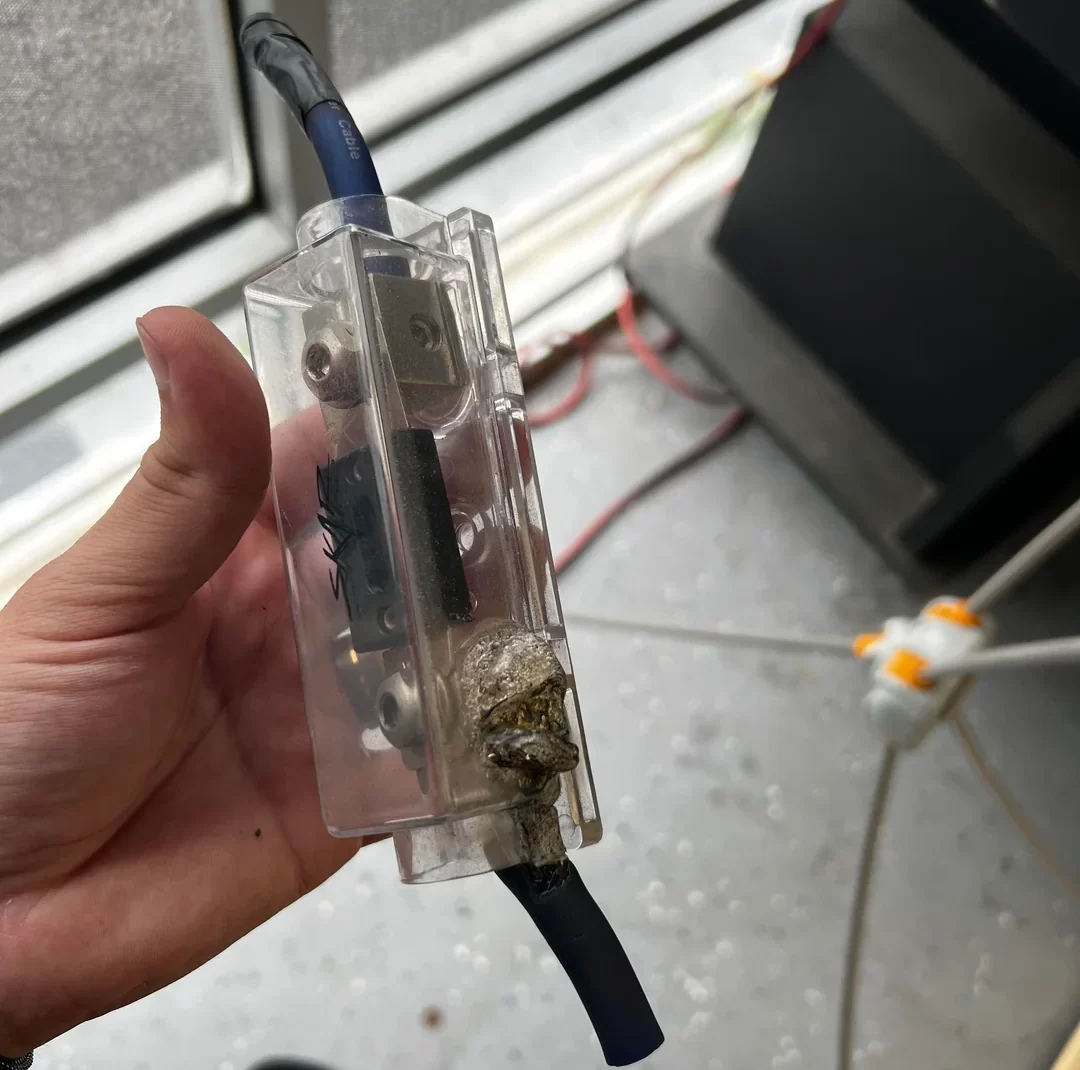
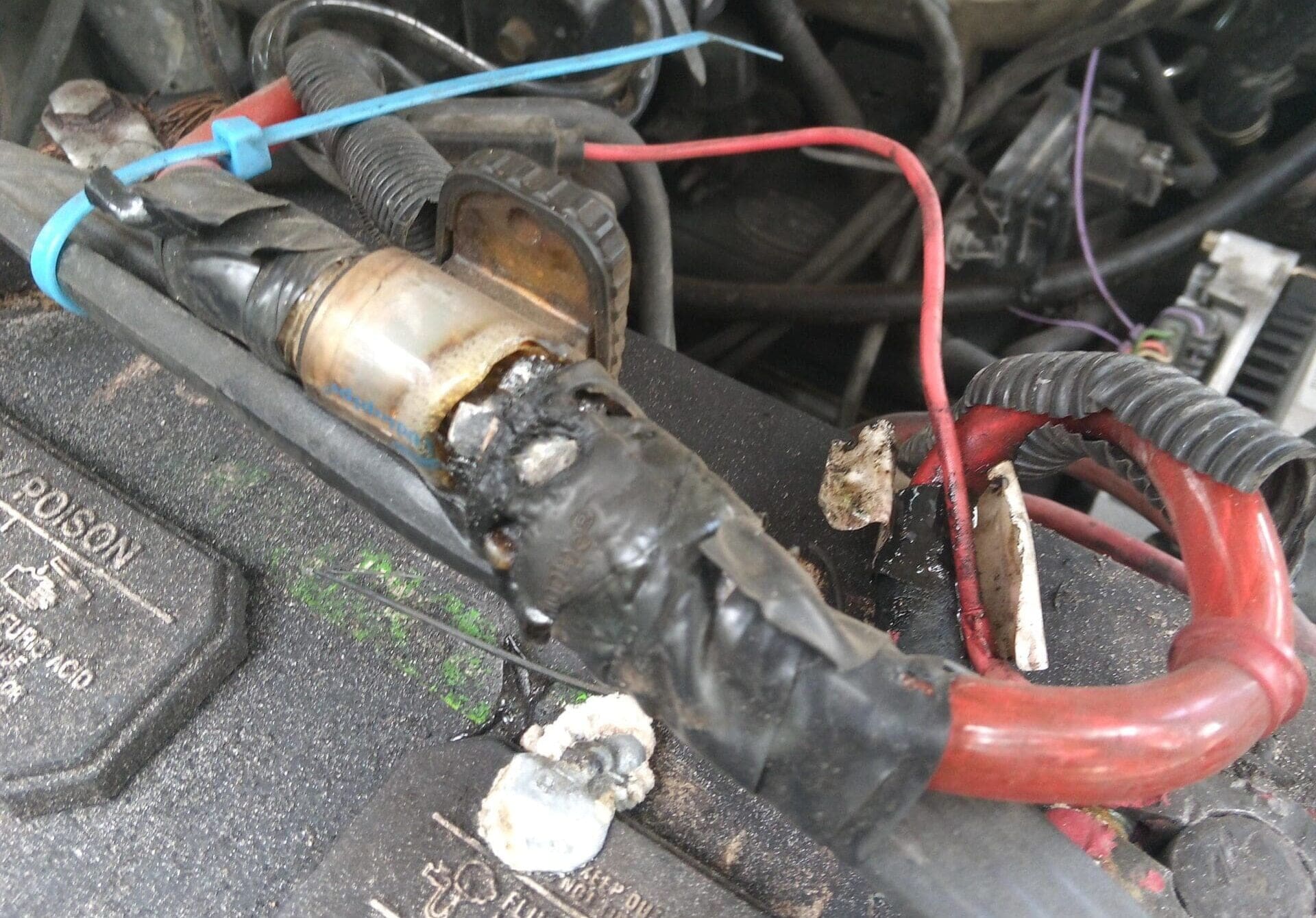
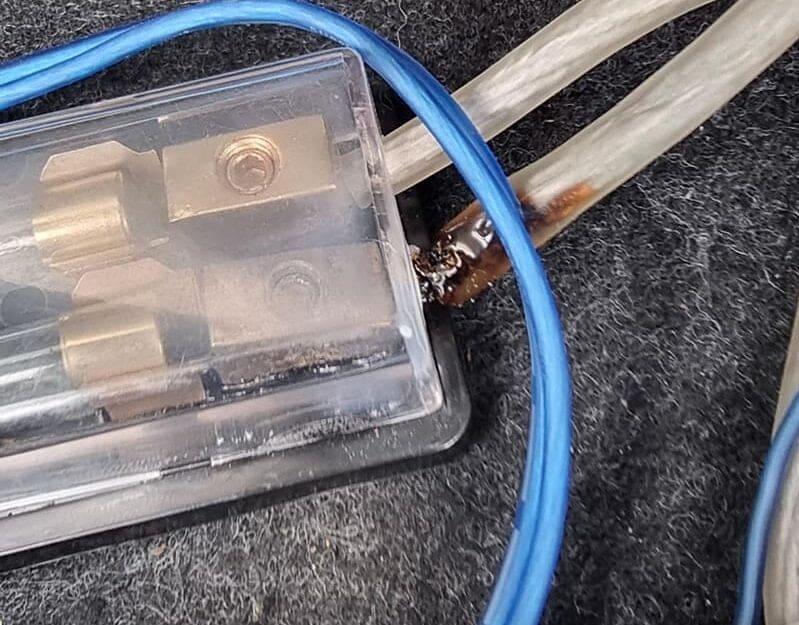
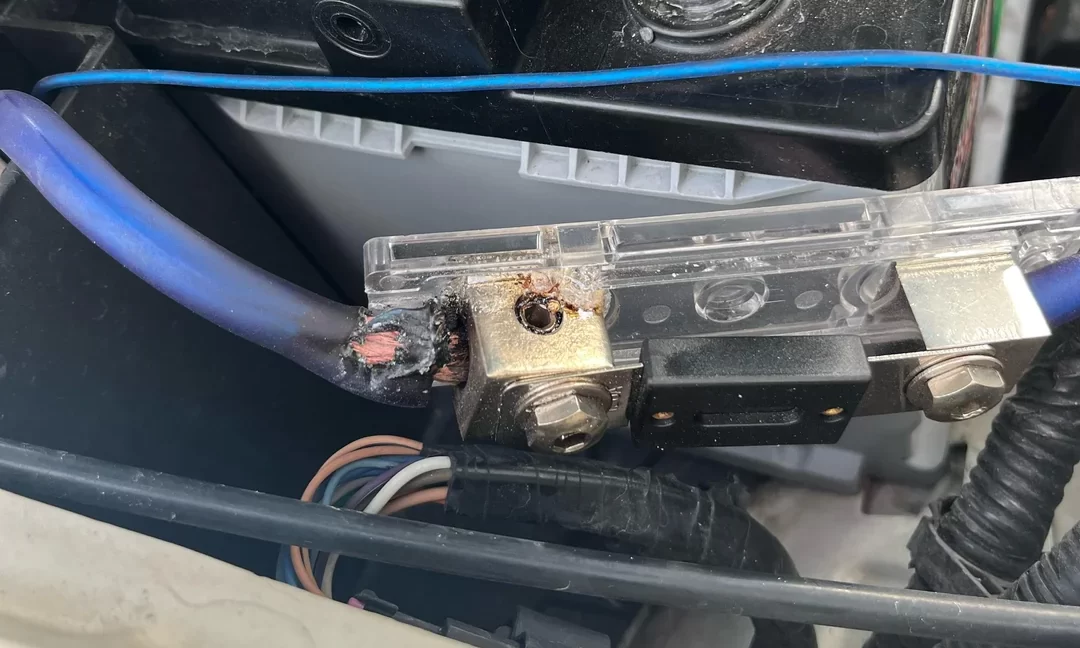
Undersized Conductors and Connections
Another reason connections fail is that the wiring and connectors are undersized. The most common place this happens is when someone uses a spring-terminal speaker wire connector on a subwoofer enclosure. The problem is exacerbated when the subwoofers are wired at low impedances and fed with a lot of power. We’ve created an entire article that discusses these connections if you want to learn more.
Quite simply, the size of the wire that fits into these connectors, the size of the terminals, and the quick-connect terminals on the inside of the enclosure have too much resistance to handle large amounts of current. Remember, the power dissipated in a connection is proportional to the square of the current times the resistance: P = I² x R.
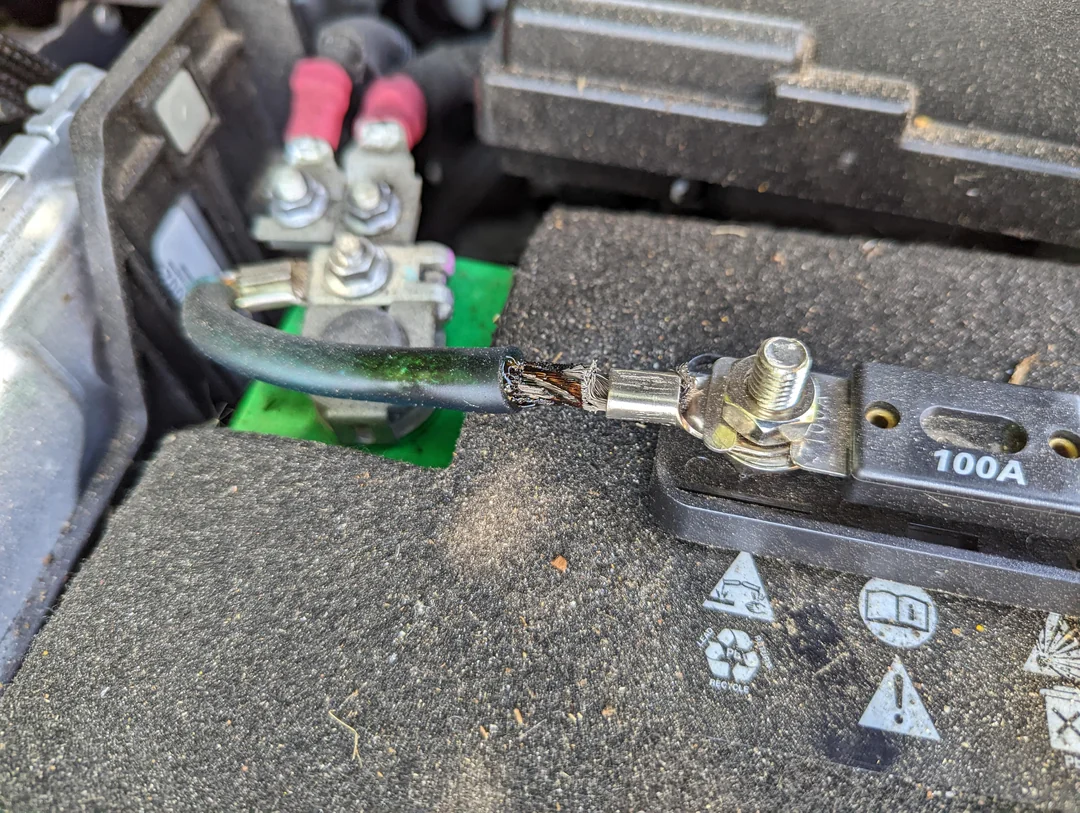
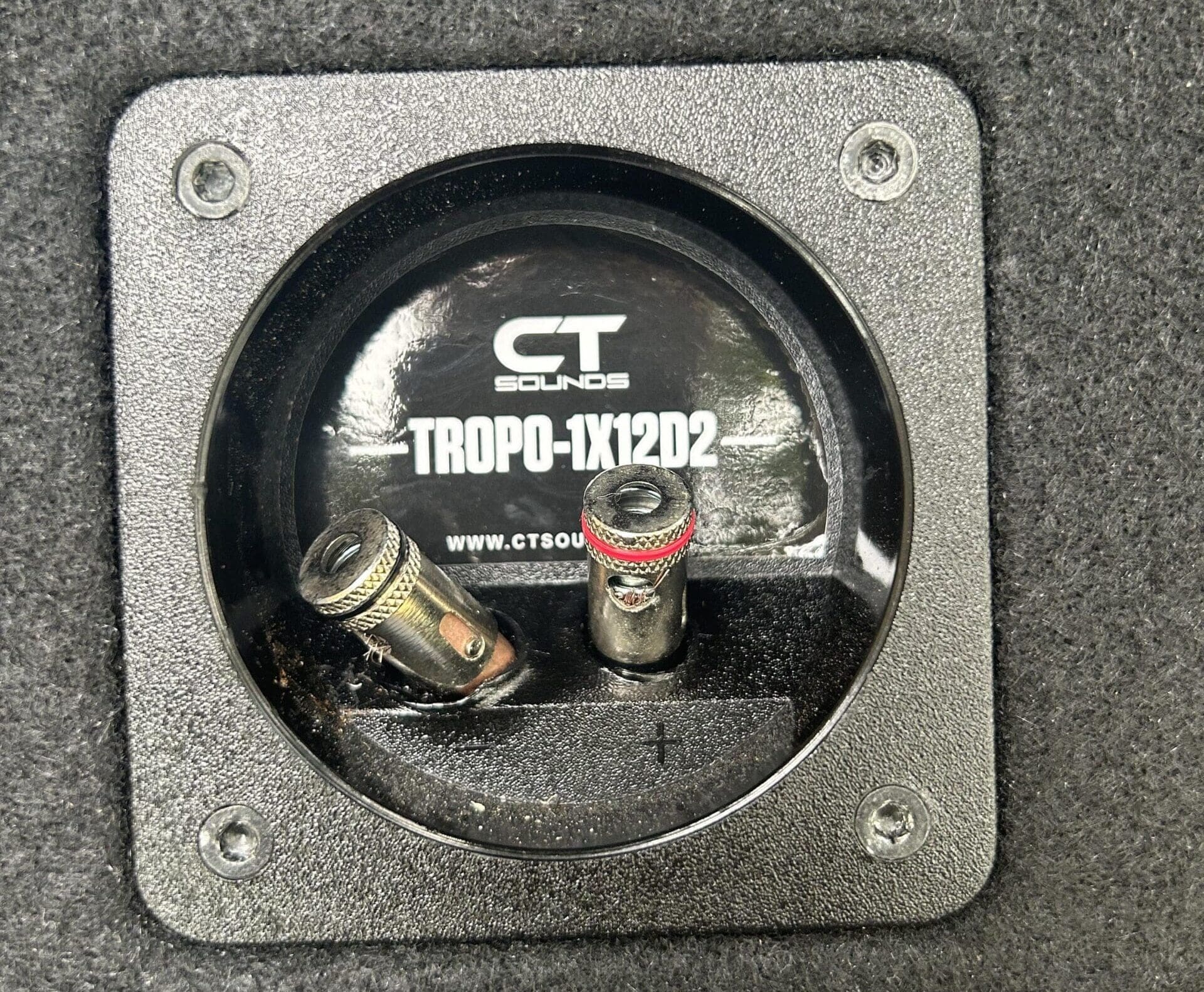
Corrosion in Harsh Climates
If your vehicle has had an aftermarket sound system for several years, corrosion may become a problem. Corrosive chemicals, like the salt used to prevent ice from forming on the road in winter, can damage and degrade the connections to the battery and the amplifier ground. However, if you live in Texas or Nevada, road salt will pose much less of a problem.
Your installer should protect exposed electrical connections in some way. For example, high-quality fuse holders usually include several O-rings to keep water out. They can protect battery terminals with CRC Battery Terminal Protector coating, which seals the metal and guards it against exposure to liquids. Similarly, protect the ground connection in a vehicle with a similar coating. If they bolt the ground through a part of the chassis, make sure to protect both sides.
Thermal Expansion
The last suggestion about why some connections have issues is somewhat hypothetical. Based on decades of working on all types of car audio installations, we’ve seen concrete evidence that lower-quality wiring increases the chances of experiencing bad connections. The low-cost wire is often copper-clad aluminum, not solid or tinned copper. Truthfully, the issue is usually corrosion-related; however, we have another theory.
Why is this the case? Our theory is that differences in thermal expansion rates in the associated materials might cause the problem. For example, copper has a thermal expansion rate of 16.5 micrometers per meter per degree Celsius. So, if you have 1 meter of copper at 17 degrees C, and raise it to 27 degrees, the copper will be 1.000165 meters long. You likely can’t measure that without a large vernier caliper. Now, what if a connection gets good and hot? Say something is slightly loose, and it jumps to 60 degrees due to the resistance in the connection. Our one-meter length of copper would be 1.00099 meters long.
Drawbacks of Copper Clad Aluminum Wire
Now, think about this. Copper-clad aluminum wire is typically mostly aluminum wire with a copper layer wrapped around the outside. Firstly, the manufacturer twists the wires together into a strand. Next, they wrap multiple strands together to achieve the conductor size you need, hopefully. Given that copper and aluminum have dissimilar thermal expansion rates of 16.5 micrometers and 23 micrometers, each wire in each strand bundle inevitably pulls the copper apart as it heats up. The aluminum stretches 39.4% more than the copper inside it.
It’s not like the aluminum will rip the copper off, as the total changes in length and diameter are very small. Nevertheless, the wire will grow and shrink over time and many heat cycles. Consequently, we hypothesize that expansion and contraction can cause the connection to loosen – even if it’s just a few dozen microns at a time. Over time, it starts to add up.”
These same expansions and contractions happen with lead battery terminals where they connect to the wire. Similarly, this can also occur with brass, aluminum, or die-cast zinc fuse holders and amplifier terminals. Specifically regarding the use of Copper-Clad Aluminum (CCA) wire, we strongly suggest avoiding it.
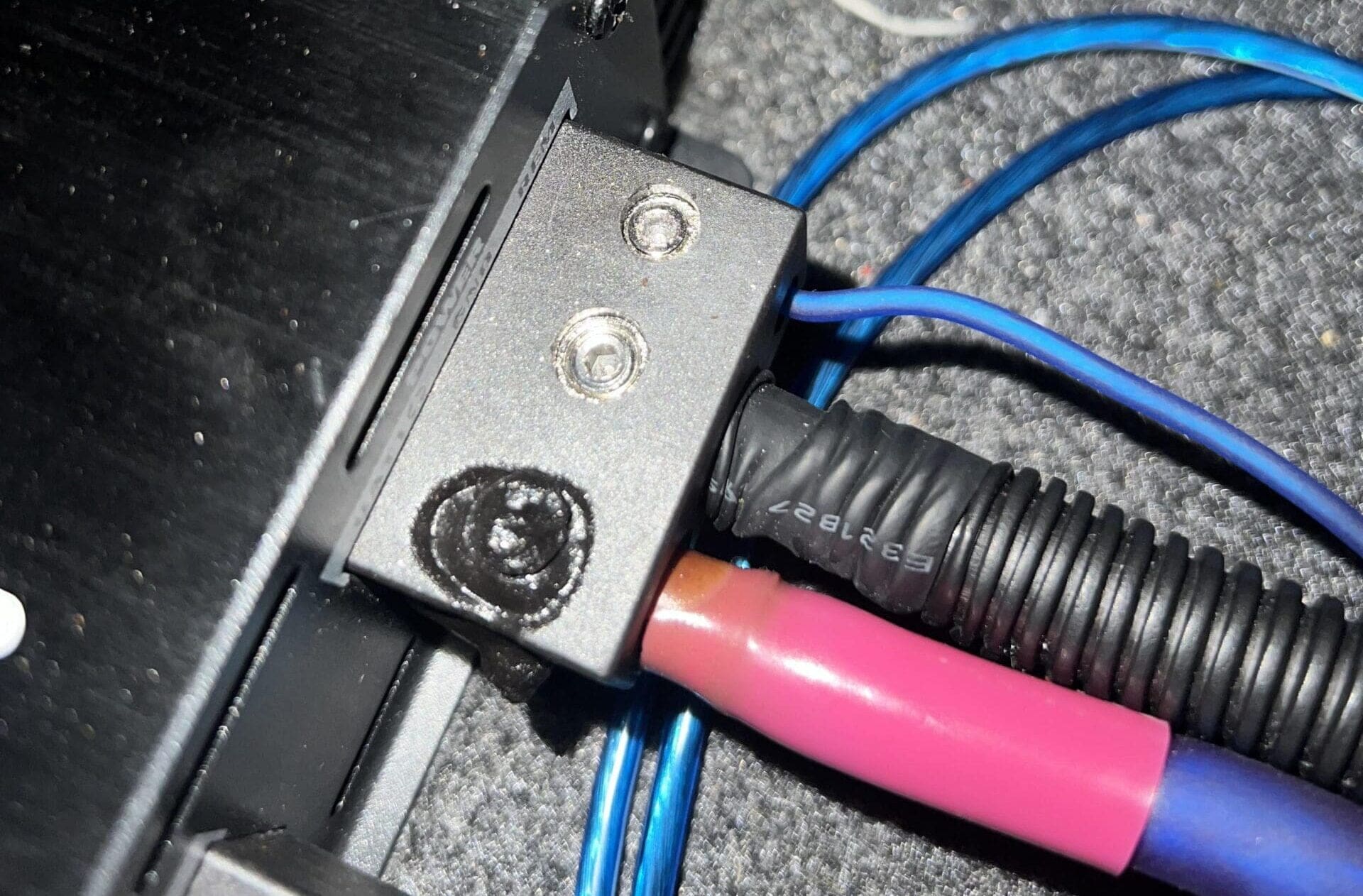
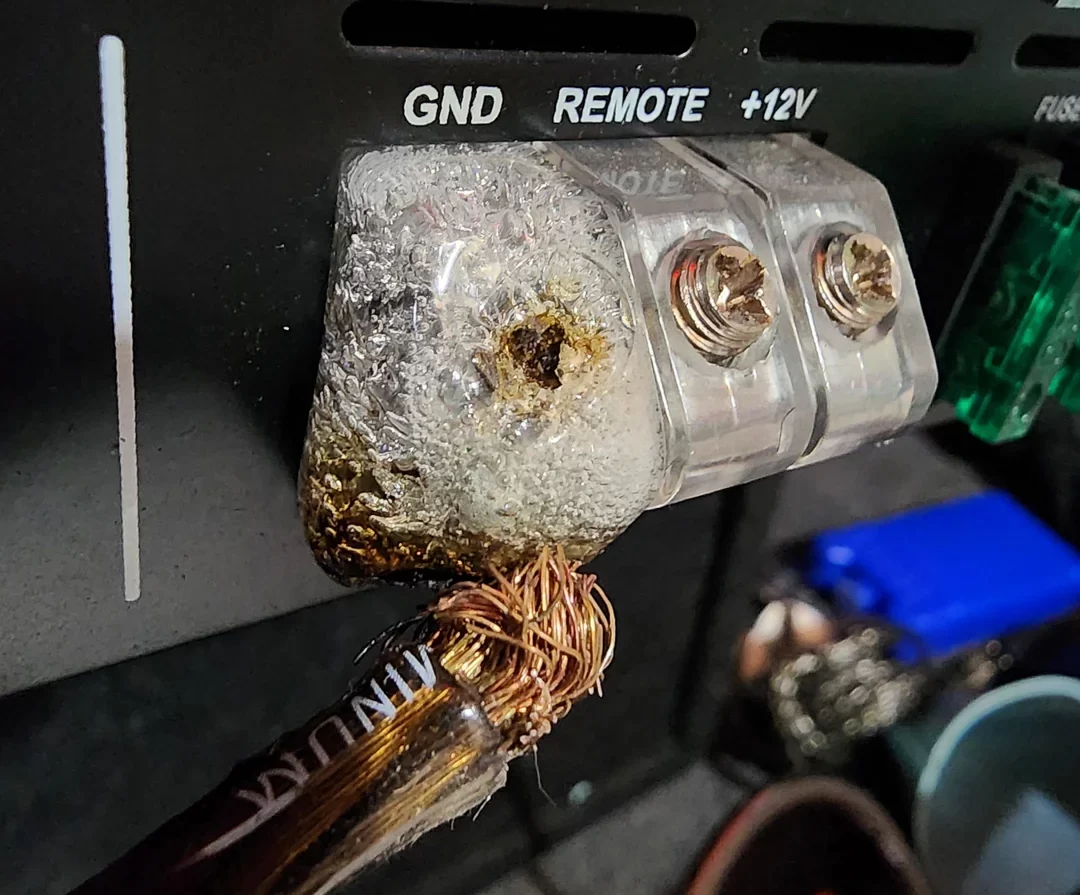
How to Prevent Loose Wire Connections
Putting all the science and math aside, the only way to ensure that every electrical connection in your car audio system is solid and secure is to have it checked. Scheduling a check-up appointment with the shop that performed the installation every few years might sound crazy in concept. Still, it’s the only way to ensure everything is safe and secure, short of welding every connection together.